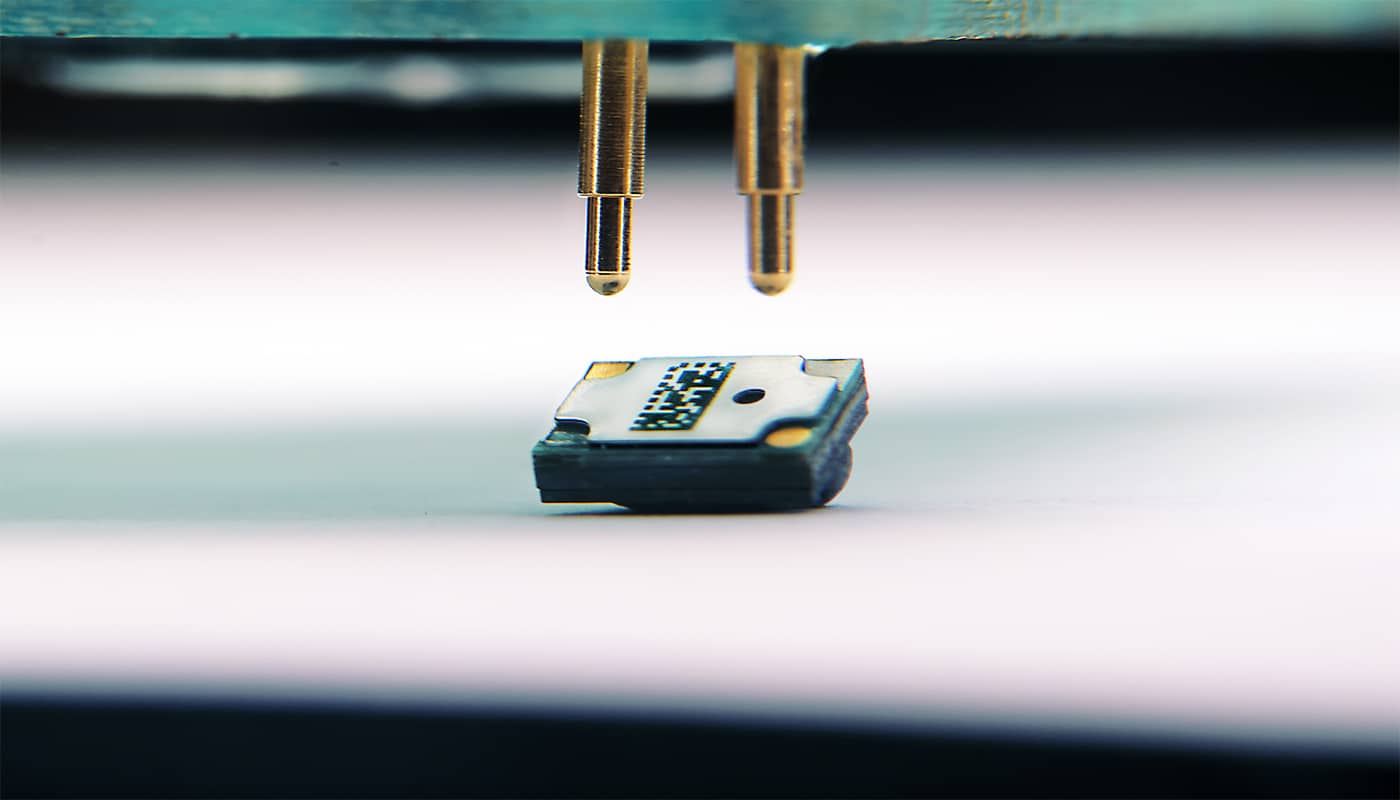
Published:
Mechanical and electrical integration of USound MEMS speakers
One of the significant advantages of MEMS speakers is the possibility to be easily integrated into a wide variety of products. Due to the very small form factor, MEMS speakers can be used in technologies requiring more minimal designs, such as TWS, audio glasses and ultrasound applications. This article will go through some essential aspects concerning the electrical and mechanical integration of MEMS loudspeakers that are of fundamental importance to obtain the best possible results.
Electrical integration
The Ganymede series of MEMS speakers all have the same connection pads on the backside. The pads are shaped differently to mark the polarity of the connection.
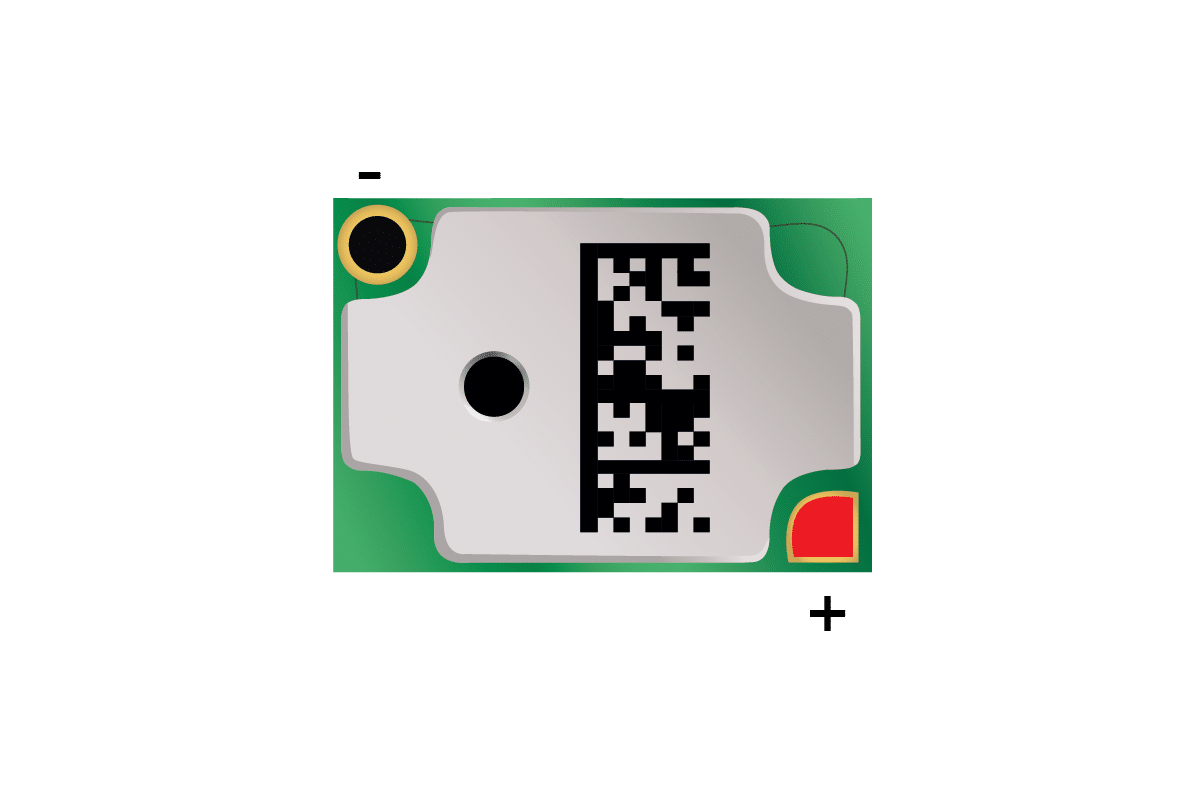
Several options are possible for electrically connecting the speakers to the system:
- Manual soldering on the pads – when soldering MEMS speakers manually, we recommend using thin soldering iron tips to avoid heating the whole loudspeaker and damaging it.
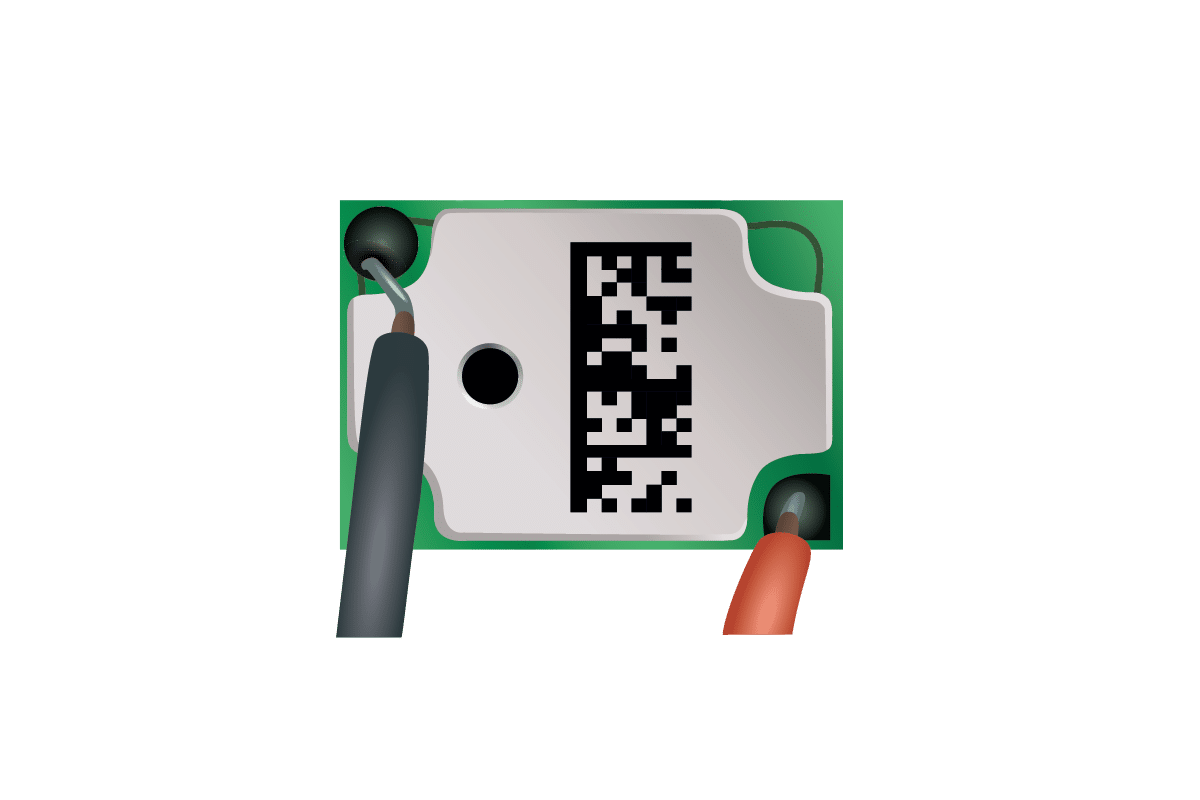
- Pogo pins or spring contacts – the pads on USound loudspeakers are compatible with spring contact or pogo pin connections. Due to the pad size, some tolerances in the design can be compensated that way.
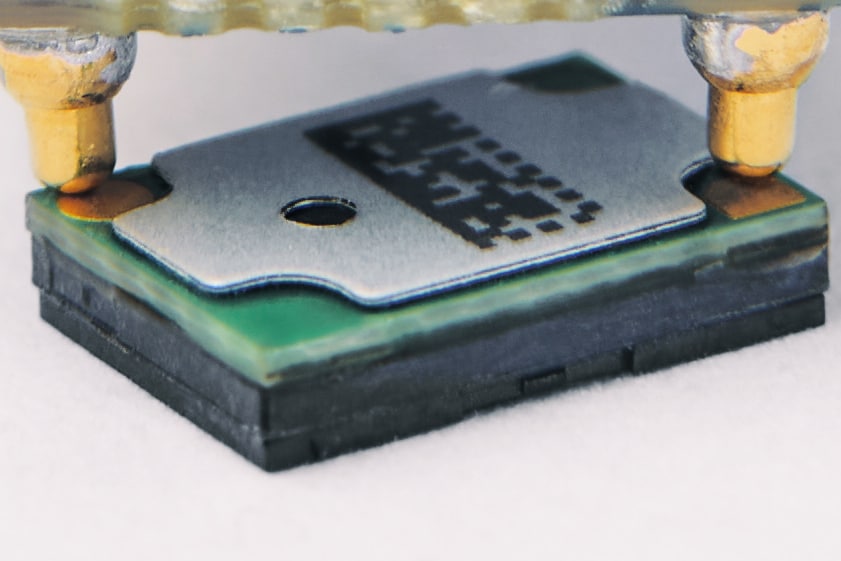
- Electrically conductive adhesive – conductive glue provides more freedom to connect MEMS speakers electrically. When using glue, make sure not to obstruct the hole on the back of the loudspeaker in order not to affect its acoustic performance.
- Reflow soldering – in general, USound MEMS speaker technology is compatible with standard SMT reflow soldering processes. With the 1st generation of MEMS speakers – Adap and Achelous – a positive case study showcasing the compatibility was done, whereas starting from the 2nd generation all USound speakers will have the reflow soldering capability.
Mechanical integration
The mechanical integration of MEMS speakers is as important as the electrical integration to achieve the highest sound quality. Sealing the front volume from the backside of the speaker is critical to obtain the best acoustic output. This can be achieved with three methods:
- Glue – one option is to glue the speaker into the application’s housing. In this case, the adhesive can be applied around the speaker or on the cover. The glueing process must be executed with care to obtain a fully sealed glue-line and not cover critical parts such as the diaphragm, the back opening or any electric contacts.
- Gasket – another option is to place a gasket between the housing and the speaker’s cover. In this case, the speaker must be pressed from the backside onto a gasket in the housing. This can be done by a mechanical feature or pogo pins/spring contacts for the electrical connection.
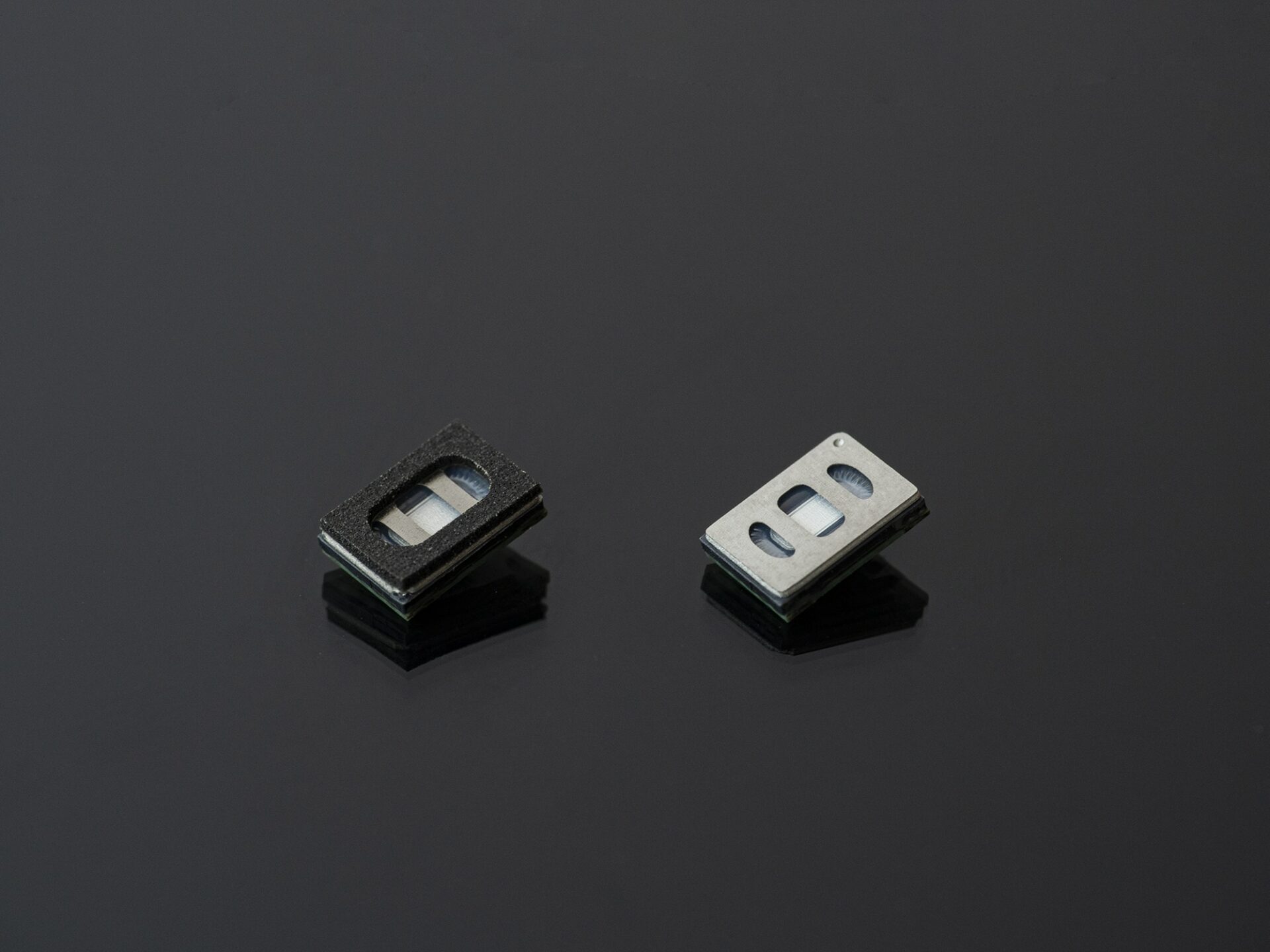
- Glue and gasket – it is also possible to use a combination of the two methods above to obtain the system’s perfect seal.
To reduce manufacturing costs, using glue may be the desired method. Yet, the usage of a gasket offers the advantage of compensating mechanical tolerances as well as the possibility of non-destructive disassembling.
To summarize, both mechanical and electrical integration are key aspects in order to achieve optimal acoustical results from the loudspeakers. Thanks to the extensive internal research in both MEMS loudspeakers and reference designs, USound provides full customer support on the integration of USound MEMS loudspeakers in many applications, such as in-ear headphones, speaker arrays and audio glasses.
Get started.
Contact us and discover how MEMS speakers can take your design to the next level.
Contact us >
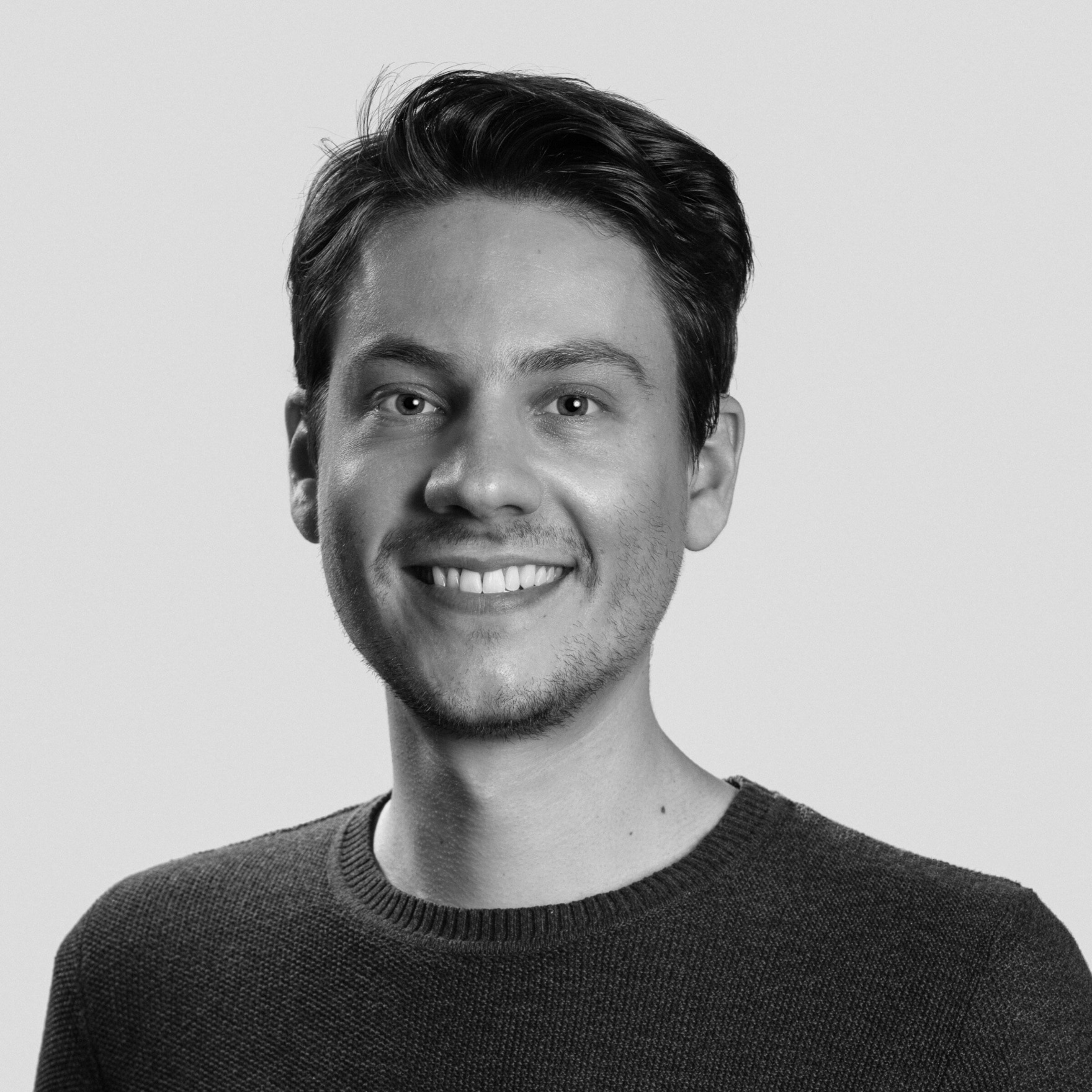
About the author
Marco Rinaldi is a Technical Sales Engineer at USound. With a background in Mechanical Engineering and Sound Engineering, he now provides customer support on the integration of USound MEMS loudspeakers.