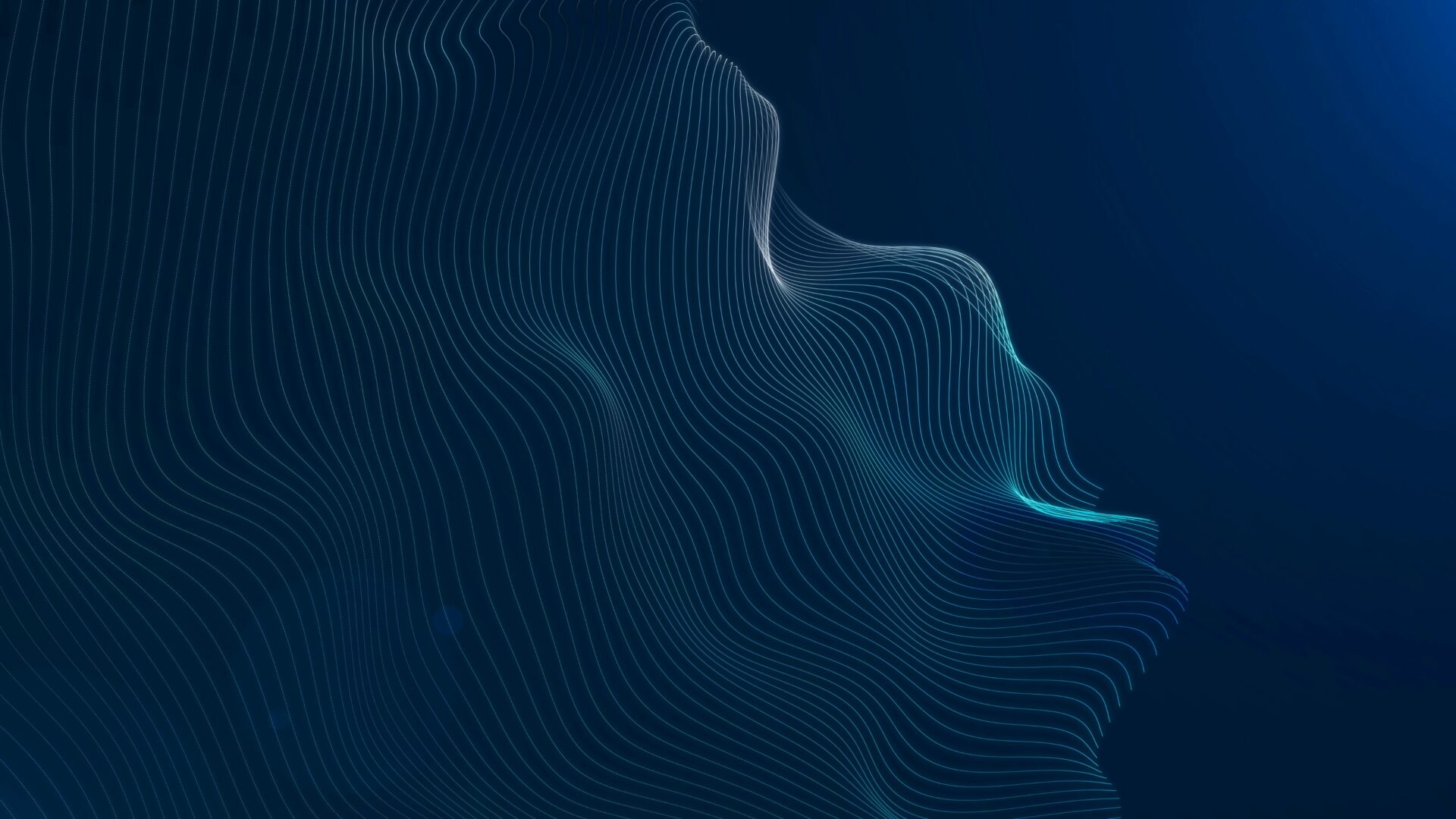
Published:
Ultrasound: The Ultimate Application for USound MEMS Speakers
Ultrasonic technology, making use of sound waves beyond the range of human hearing, has revolutionized various scientific fields. From healthcare to manufacturing, to consumer electronics, ultrasonic applications have propelled innovation and efficiency. As technology continues to advance rapidly, the applications of ultrasonics are going to expand further, driving innovation and addressing complex challenges across various domains.
This article explores the multifaceted world of ultrasonic applications, where sound waves unlock a realm of opportunities for scientific discovery and practical solutions. MEMS speakers are paving the way to a whole new range of technological possibilities, with ultrasonics being one of the key areas where this type of speaker will shine.
Definition
The American National Standard on Acoustical Terminology defines Ultrasound as “sound at frequencies greater than 20 kHz, [which] is the limit of the approximate upper range of human hearing”. Similarly, Ultrasonics is defined as the “technology of sound at frequencies greater than 20 kHz”. The term “ultrasonic” is therefore meant to be used as an adjective to indicate a component, a device or a system intended to operate in the ultrasound frequency range.
Depending on the listener age, health status and hearing capabilities, high frequency sounds and even ultrasounds in the lower frequency range can be audible if the sound level is high enough. Nevertheless, the 20 kHz limit is far from being commonly reached, since such high frequencies can only be heard by healthy children and young adults.
Ultrasonic devices operate with frequencies from 20 kHz up to several gigahertz, depending on the intended application: for example, sonochemistry uses frequencies up to few hundreds of kilohertz, while medical imaging equipment uses frequencies in the MHz range and UHF can reach the gigahertz range.
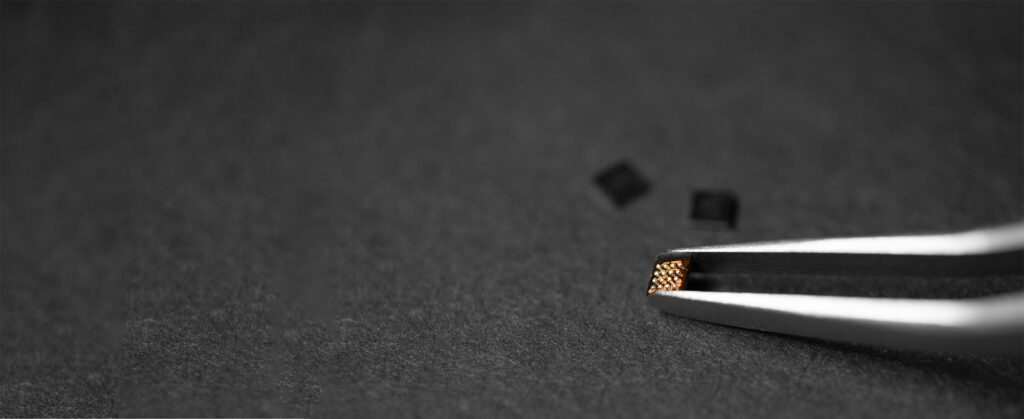
Exposure Limits
The International Non-Ionizing Radiation Committee (INIRC/IRPA, 1984) has imposed certain occupational exposure limits for high-frequency sounds (16-20kHz). The committee has also provided exposure limits for the general public (70 dB < 20 kHz and 100 dB >25 kHz). These are the recommendations provided to the World Health Organization. Respecting these limits would offer protection against subjective effects and possible hearing loss as a result of protracted exposure. The current research is neither definitive or comprehensive, and further studies are required to assess the ultrasounds effects on human beings.
Ultrasonic applications
Ultrasounds are nowadays used already in several fields, including physics, engineering, medicine, and materials science. Ultrasonics can be used to detect objects and measure distances, as a diagnostic or therapeutic tool, as a non-destructive testing tool for products and structures, as a safe mean for cleaning, mixing, and accelerating chemical processes, and many more.
Here is a brief description of the main applications using ultrasounds:
- Medical Imaging: ultrasonography, or ultrasound imaging, is used for diagnostic purposes in medicine, allowing visualization of internal organs and tissues without ionizing radiation. It is widely used in obstetrics, cardiology, oncology, and many other medical fields.
- Surgery and Therapy: ultrasounds can be used for therapeutic applications in medicine, with different effects depending on their intensity level. Ultrasonic technology is commonly used in surgical procedures for cutting, ablation, and tissue dissection, as well as in therapeutic applications such as physiotherapy, fracture repair, sonophoresis, sonoporation, gene therapy, lithotripsy (breaking kidney stones) and even for cancer treatment.
- Non-Destructive Testing: employed in industries such as aerospace, automotive, and manufacturing to inspect materials and structures for defects, cracks, or irregularities without causing damage to the tested objects.
- Cleaning and Processing: ultrasonic cleaning utilizes high-frequency sound waves to remove dirt, contaminants, and residues from surfaces, instruments, and delicate components. Ultrasonics are also used in processes such as emulsification, dispersion, and degassing in various industrial applications.
- Sonar and Underwater Communication: ultrasonic devices are utilized in sonar systems for underwater navigation, detection of objects, and communication in marine environments.
- Material Characterization: ultrasounds are employed to analyse the properties of materials, including their density, elasticity, thickness, and structural integrity, through techniques such as ultrasonic spectroscopy and ultrasonic tomography.
- Environmental protection: ultrasounds can also be used for the purification of water, the treatment of sewage sludge, the decontamination of the atmosphere and soil remediation.
Ultrasonics continues to be an active area of research and innovation, with ongoing advancements in transducer technology, signal processing techniques, and applications across diverse fields, such as – but not limited to – the ones described above.
Ultrasonic devices
To produce ultrasound waves, several electronic components are required to generate and control frequency, amplitude, and timing of the signal. The systems designed to generate ultrasounds are referred to as “ultrasonic devices” and are typically made of the following components:
- Ultrasonic Transducer: core component responsible for converting electrical energy into ultrasounds and vice versa.
- Signal generator: produces the high-frequency electrical signals that drive the ultrasonic transducer. These signals can be in the range of tens of kilohertz to several gigahertz, depending on the application.
- Amplification stage: amplifies the signals coming from the signal generator to levels sufficient to drive the ultrasonic transducer. It ensures that the transducer receives the required power to produce output signals with the desired sound level.
- Control circuitry: responsible for managing the overall behaviour and performance of the system. It includes microcontrollers, digital signal processors (DSPs) and application-specific integrated circuits (ASIC) designed and programmed to control the timing, amplitude, frequency, and duration of the ultrasound signals.
- Power supply: provides the necessary electrical energy to the different system components. It may be AC-powered or battery-powered, depending on the application requirements.
- Receiver circuit: in applications where ultrasounds are used for sensing or detection, a receiver circuit is required to process the electrical signals generated by the ultrasonic transducer and reflected back to the system after interacting with the environment.
These electronic components work together to form an ultrasonic system capable of generating, controlling, and detecting ultrasonic waves for various applications, including imaging, distance measurement, proximity sensing, non-destructive testing, and so on. The specific design and configuration of the system depend on the requirements of the application and the desired performance.
Ultrasonic transducers
A device which is specifically intended to work with ultrasounds is called ultrasonic transducer. A transducer can work in both directions, using its material properties to either generate or to detect ultrasounds. The choice of the right transducer to generate ultrasounds depends on the specific requirements of the application, including frequency range, acoustic output, power consumption, size constraints, efficiency, reliability, and cost. Additionally, it’s important to ensure that the chosen transducer is compatible with the electronic circuitry and the signal processing requirements of the application.
There are two fundamental transducer designs used today for ultrasonic applications:
- Piezoelectric: these transducers utilize the piezoelectric property of a material to convert electrical energy into mechanical vibrations. They are available in various form factors, including discs, plates, horns, and can operate at ultrasonic frequencies ranging from tens of kilohertz to several megahertz. Piezoelectric transducers are characterised by high efficiency, low distortion, and precise frequency control.
- Magnetostrictive: these transducers exploit a particular property of ferromagnetic materials called “magnetostriction effect” that causes them to change their shape when subjected to a magnetic field provided by a coil of wire which is wrapped around the magnetostrictive material. Similarly to the previous case, this effect allows these materials to convert electrical energy into mechanical vibrations. They typically operate at lower frequencies compared to piezoelectric transducers but may offer advantages in specific applications.
Power consumption
The power consumption required to drive ultrasonic transducers depends on several factors, including the frequency range and the amplitude of the signal, the duty cycle, and the size and design of the transducer. Here are some considerations regarding the above-mentioned factors:
- Frequency range: ultrasounds typically require more power compared to audio frequencies. This is because higher frequencies mean faster oscillations of the transducer material, hence more energy. Also, at higher frequency, the transducer impedance is usually low, which translates into a higher power consumption.
- Signal amplitude: ultrasound waves amplitude has an impact on the system power consumption. Higher amplitude waves will require more power to generate compared to lower amplitude waves.
- Duty cycle: refers to the percentage of time that the ultrasonic system is active versus idle. Continuous operation at high-duty cycles consumes more power compared to lower-duty cycles or to intermittent operation.
- Transducer size and design: with a certain material and stack-up, larger transducers may require more power to achieve the desired ultrasonic intensity. Additionally, the design efficiency of the transducer, including factors such as resonance frequency and type of load (e.g., resistive or capacitive), can affect power consumption.
- Electronic efficiency: the efficiency of the electronic components used to drive the ultrasonic transducer, including the signal generator, the amplifier and the power supply, will also have an impact on power consumption. More efficient electronics will consume less power for the same output.
Overall, the power consumption of an ultrasonic system can vary widely depending on the previously described factors and the specific requirements of the application. It’s essential to carefully design and optimize the system to balance performance with power efficiency, especially in portable or battery-powered applications where power consumption is a crucial parameter in the system design.
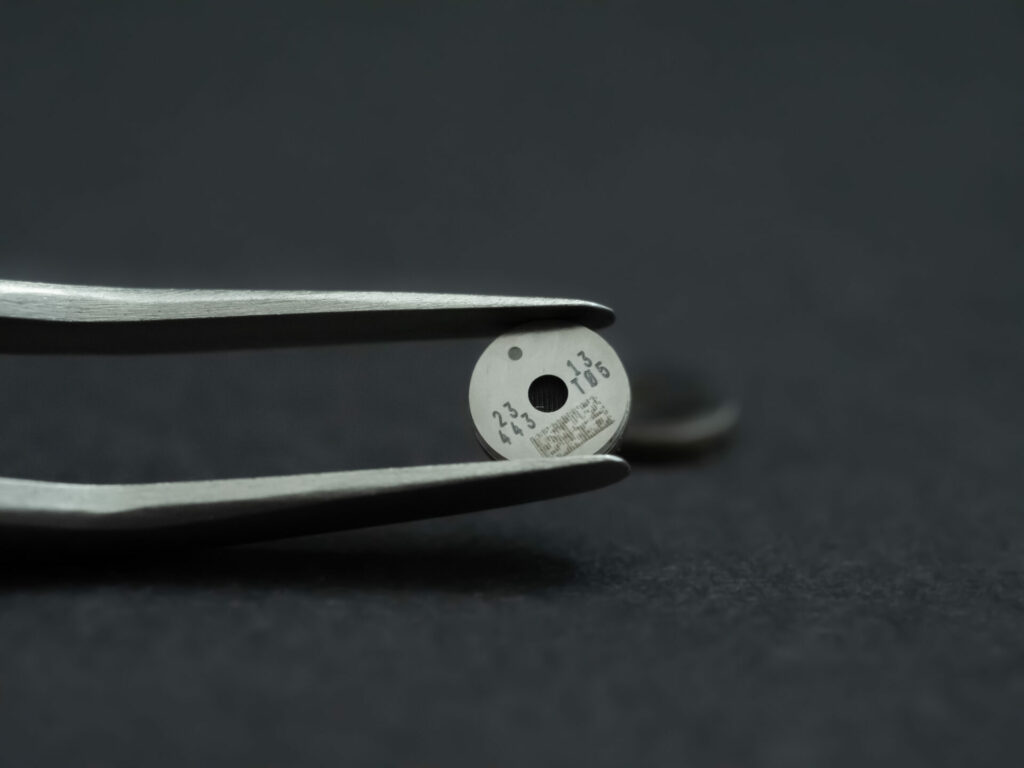
Typical ultrasonic application: proximity sensing
Proximity sensing is a technology that utilizes ultrasound waves to detect the presence or proximity of objects within a certain range from a device. This technology is commonly used in various fields, including robotics, automotive systems, industrial automation and consumer electronics.
Here’s how ultrasound proximity sensing typically works.
The system includes at least one ultrasonic transducer that acts as both a transmitter, which sends ultrasound waves into the surrounding environment, and a receiver, which detects the waves reflected back from nearby objects. The transducer emits short ultrasound bursts at regular intervals (Pulse-Echo); these waves travel through the air until they encounter an object along their path and are reflected back towards the transducer. By measuring the time that it takes for the wave to travel from the transmitter to the object and back to the receiver (Time-of-Flight), the system measures the corresponding distance from the device, determining whether the intercepted object falls within the predefined proximity range. If this is the case, the system triggers a response or takes appropriate action, such as activating an alarm, playing a sound, adjusting the properties of the device, activating or deactivating the system, and so on. Parameters such as the frequency and amplitude of the ultrasound waves, environmental conditions (e.g., temperature, humidity), and the properties of the objects being detected (e.g., size, shape, material) can affect the accuracy and reliability of ultrasonic proximity sensing.
Ultrasonic proximity sensors have several advantages, including:
- Non-contact operation: ultrasonic devices can detect distant objects (within a limited range) without physical contact, making them suitable for applications where contact sensors are impractical or undesirable.
- Sensing distance: ultrasonic sensors can detect objects at distances ranging from a few centimetres to several meters, depending on the design and configuration of the system and the type and characteristics of the transducer.
- Immunity to colour: unlike optical sensors, ultrasonic sensors are not affected by the colour, transparency, or surface characteristics of the detected objects, making them versatile in various environments.
In a nutshell, ultrasonic proximity sensing provides a relatively simple and effective solution for detecting objects in the surrounding area of the application device, enabling diverse and innovative applications across different industries.
Ultrasound with MEMS speakers
Consumer electronics companies are always on the lookout for new components that can be used in ultrasonic applications.
Due to their excellent audio performance at the most compact size on the market, USound MEMS speakers represent an ideal solution for ultrasonic applications: our Conamara speakers, as an example, feature an ultrawide and flat frequency response also in the ultrasound range, making them suitable for a variety of applications, including consumer electronics, smart devices, industrial applications, and home appliances.
Not having a frequency hotspot (single frequency point where the speaker can be efficiently utilized), these speakers are versatile and gives the designer a wide frequency range to choose from for its specific target application.
USound MEMS speakers are much smaller than other ultrasonic transducers. Due to their small size, they can be seamlessly integrated into miniature devices, reducing the device’s weight, while freeing-up space for additional components and sensors.
USound MEMS speakers show several advantages for ultrasonic applications:
- Compact and lightweight form factor for seamless integration into miniature devices.
- Operational frequency range up to 80 kHz and beyond.
- Flat frequency response in the ultrasound frequency range
- SMT reflow soldering for an automatic pick and place assembly.
- Extended battery life (when driven by our Tarvos audio amplifier).
- IPX8 waterproof rating.
- Drop-proof design (100% survival rate at a 1.9 m drop test).
- Low heat generation and mechanical vibrations.
- No magnetic fields.
Conclusions
You now have an overview of ultrasound technology, including its components, performance, and potential applications. Ultrasound finds extensive use across diverse fields including medicine, engineering, and materials science. Numerous studies are being carried out, showing the ongoing rapid advancements in ultrasonic technology, driven by research and innovation. In this scenario, USound MEMS speakers represent an ideal solution for ultrasonic applications, offering advantages such as compact size, operational frequency range, and performance. If you want to identify the best speakers for your ultrasonic application, feel free to talk to one of our acoustical engineering experts, who will be happy to support you and guide you through your design process.
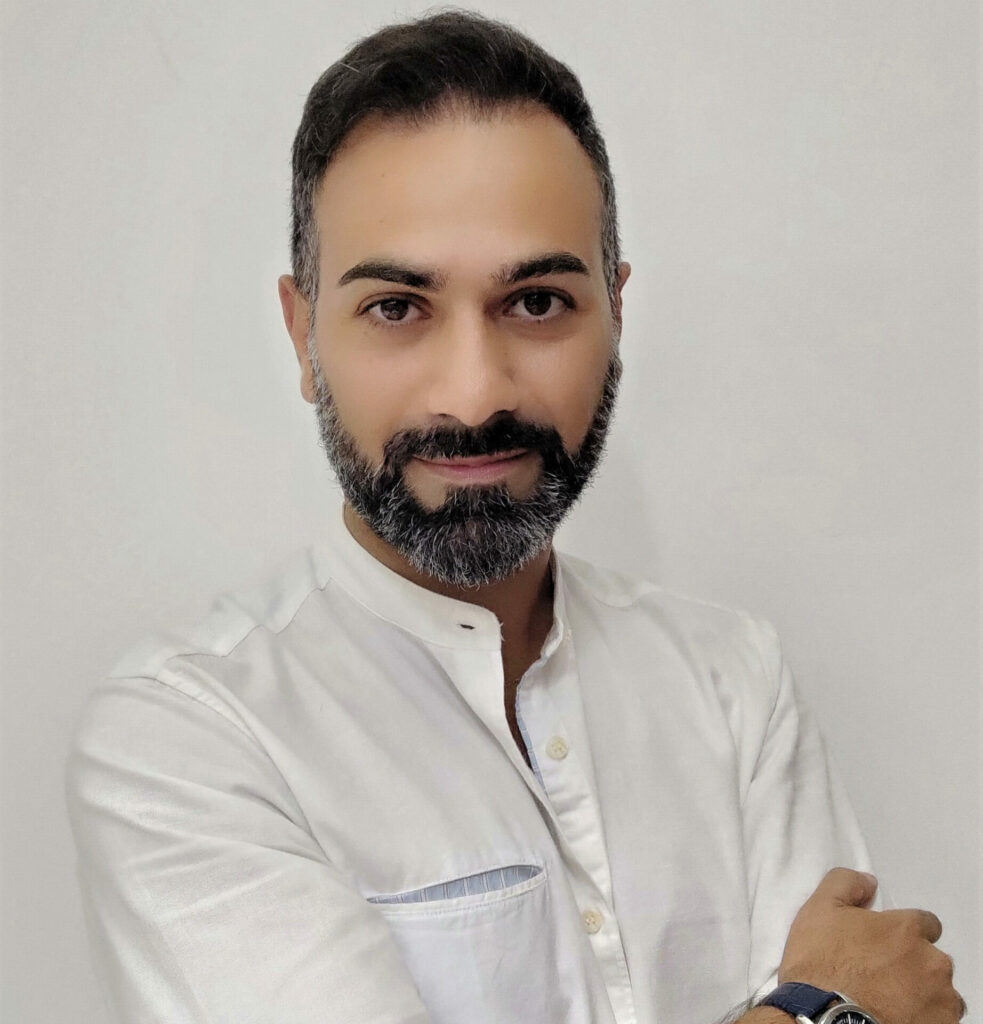
About the Author
Andrea Greco is a Field Application Engineer at USound. He has international experience as an Acoustics Engineer, with a background in both acoustics and music. LinkedIn