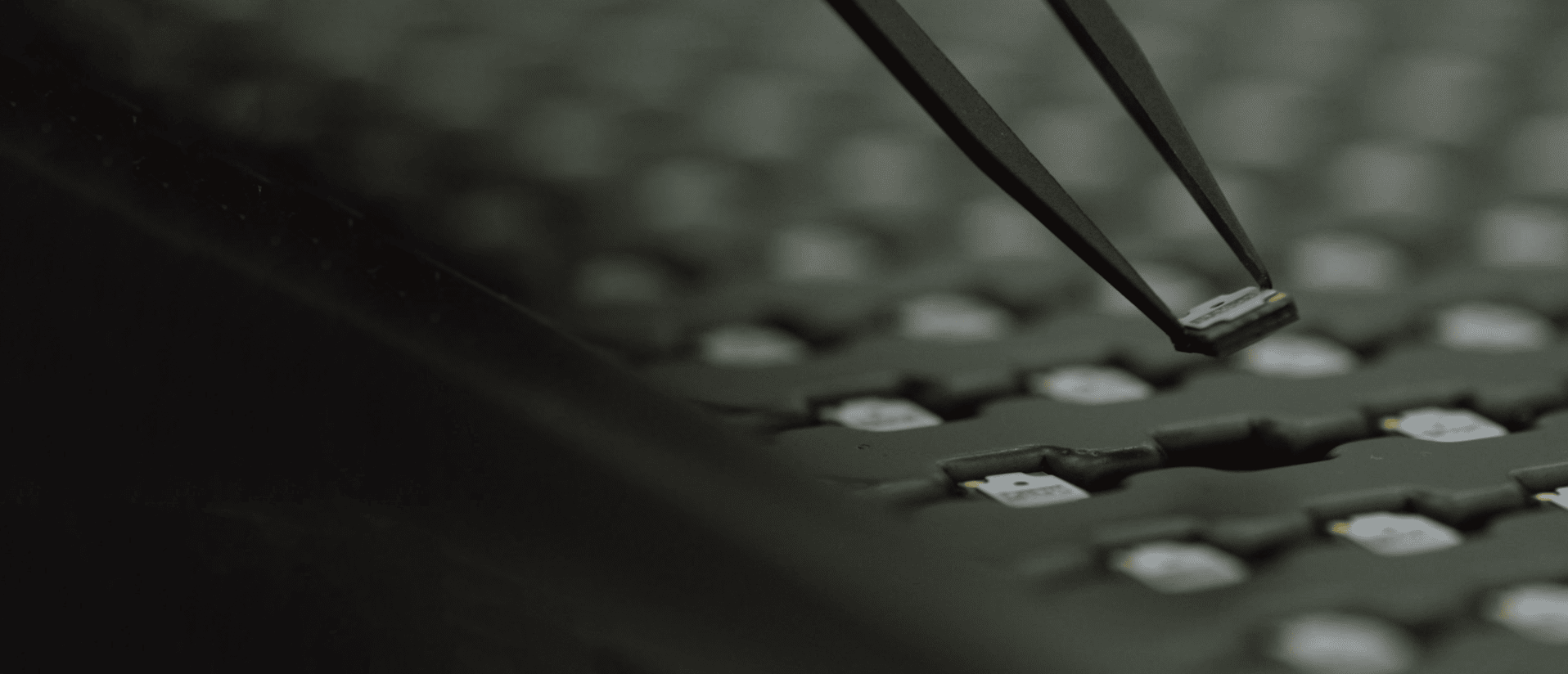
Published:
Ensuring High-Quality Standards as a Fabless Company
Designing and selling hardware, while outsourcing the fabrication process, is nothing new in the Tech industry. It is known as “fabless manufacturing”, and it is especially widespread in the field of MEMS (micro-electromechanical systems) technology. USound is no exception. The benefits of adopting the fabless model are countless: cost efficiency, flexibility, scalability, and much more. At the same time, there are many challenges, as there is limited control over the manufacturing process. How can a fabless company ensure the highest quality standards for its products?
Quality Mindset
Having the right mindset is important when it comes to establishing quality standards. Since its foundation in 2014, USound has not settled for anything less than the very best. It is our unwavering commitment to provide outstanding products that meet the highest specifications. By establishing a quality-centered mindset, fabless companies such as USound can create a detailed Quality Management plan to ensure that the standards are not only adhered to, but exceeded.
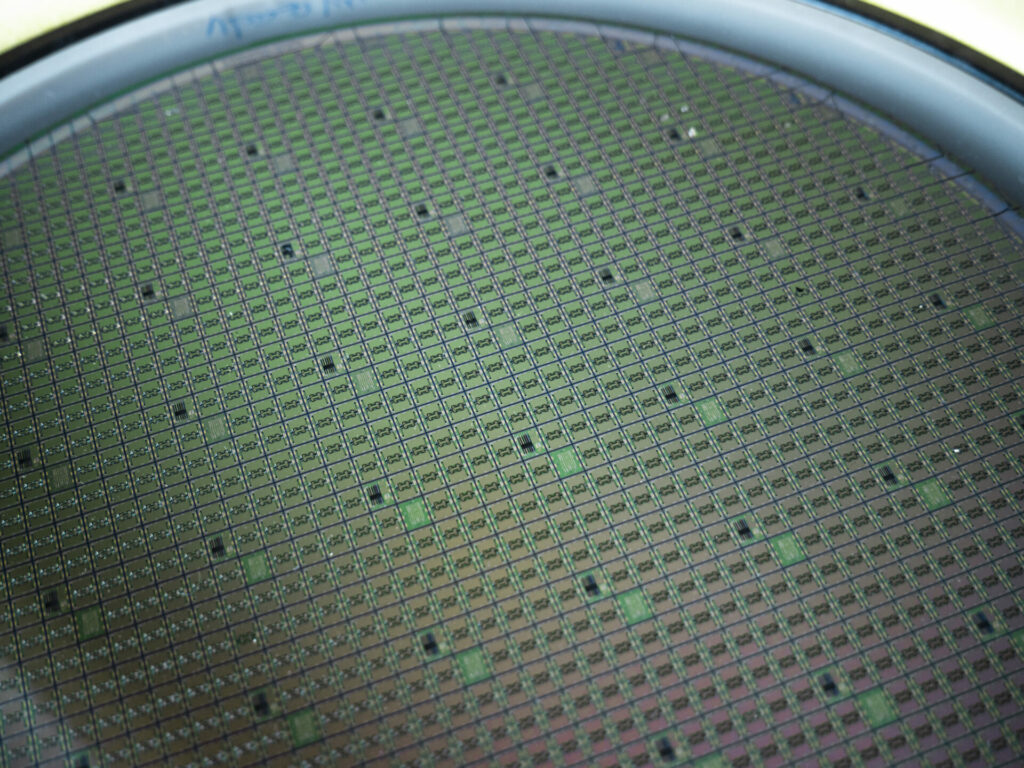
Quality Management
Quality Management is the practice of overseeing all activities and tasks needed to maintain the desired level of excellence. It includes four steps known as “Quality Planning”, “Quality Assurance” (QA), Quality Control, and Continuous Improvement. Finding a Quality Management System (QMS) is essential to follow all involved quality steps.
USound chose an interactive Quality Management System (QMS) and opted for a wiki-style platform. Our web-based QMS is designed like a wiki, making it easy to use. Everyone can access and suggest changes to all processes, promoting collaboration and continuous improvement. Having a user-friendly QMS is a must for a well-functioning quality management process. That is especially true for fabless companies in industries that are always evolving. With a high drive for innovation and rapidly changing market demands, employees need to easily access the content for quick edits and updates. Otherwise, progress can be hindered due to the inflexible and time-consuming processes.
Furthermore, our QMS comes with integrated apps. In line with our continuous improvement mindset, we are using an “Improvement App”. It allows us to trace any kind of issue in our value chain, making sure that a root cause analysis is done and closed with defining improvement actions. Within the improvement app, we use common methods, like 8D reports, the Ishikawa diagram or the 5-whys. Contributions are encouraged within the company and every employee can suggest an improvement within a few minutes.
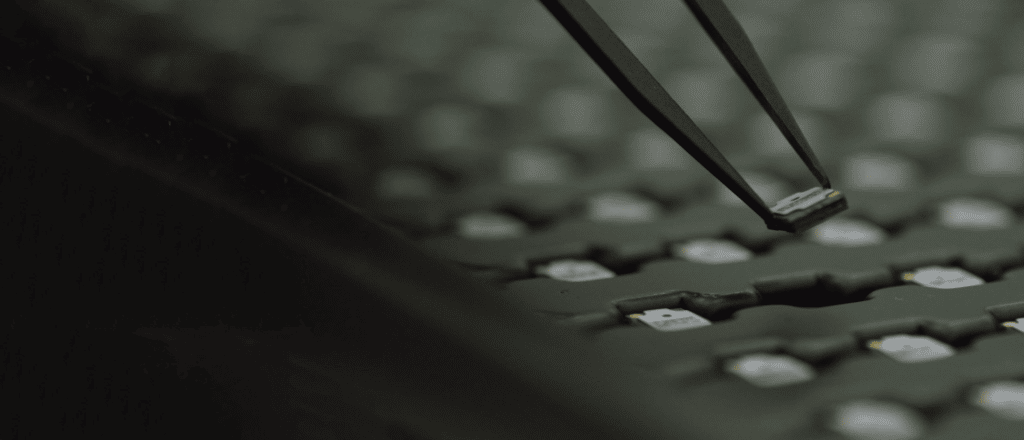
Suppliers
As USound is a fabless semiconductor company, there are different quality challenges compared to companies which are built on both pillars, design and manufacturing. Due to our fabless approach, USound applies special quality focus on external manufacturing suppliers. Maintaining a strong cooperation with our key suppliers along the value chain is very important. The same applies for resilience measures like second sources. The main selection criteria for suppliers is usually based on their technical capabilities and quality standards.
At USound, we always choose ISO 9001 certified suppliers, with an effective QMS and who meet the international standards for quality. Furthermore, to ensure clear communication with the supplier, USound has employed resident engineers in the regions where the manufacturing facilities are located. Our subsidiary in China, for example, is largely composed of engineers working in close physical proximity with our partners. Moreover, there is an auditor pool of employees who regularly conduct audits with the suppliers, to foster their development and establish a high level of QA processes.
Statistical Tools
USound employs engineers who are highly trained in statistical tools. The tools are extensively used to evaluate quality issues and improvement actions. With statistical knowledge, we can make reliable data driven decisions, reducing development time and ensuring step-by-step improvements. Our statistical tool allows us to apply various statistical analysis methods and visualizations.
Another way of ensuring that our customers receive the best quality speakers is by performing acoustical and electrical testing on all manufactured products. This helps us collect large amounts of data and filter out the products that do not fulfill our quality standards. We have developed our own test software application based on off-the-shelf tester hardware. Customized to our needs, analysis can be done in a fast and efficient way by us and our suppliers to whom we provided the software.
Product Qualification
Customer satisfaction is our primary goal, which depends on reliable products. MEMS speakers function differently from traditional speakers, presenting new challenges to enhance their reliability. Consequently, identifying and solving the underlying causes of certain issues demanded thorough testing, data-driven investigations and careful analysis.
To ensure the robustness of the products, USound performs thorough reliability tests with environmental, electrical, mechanical and combined stresses based on international standards from IEC, JEDEC or ISO. Furthermore, by applying root cause analysis, we improve our products step by step during the development.
Design Quality
Another QM aspect is design quality. Thorough design reviews are conducted to reduce the probability of errors during development and ensure that the products are fitting to our customer needs. An important part of the MEMS speaker design review is the MEMS die, as it mainly impacts the final performance and reliability of our products. With the usage of multiple analytical and numerical simulations, we have accelerated development times and have a well-fitting outlook of the manufactured pieces.
Ensuring high-quality standards as a fabless company requires an extensive and detailed QM plan and continuous communication with the manufacturing partners. Establishing a quality mindset within the team and finding the right QMS platform and testing solutions are crucial for providing products of excellent quality.
If you are interested in obtaining USound’ s solutions for advanced audio systems, contact us and one of our experts will assist you.

About the Author
USound’s broad-knowledge expert on industrialization, development, and application support, Markus Bartek drives USound’s innovations, with a background in Electrical engineering and over 10 years’ experience in the Audio industry. He has been with USound since 2014. LinkedIn